Pull rolls
Pull rolls are driven and will be used for web transport. Thereby pull rolls are used for tension separation before and after these rolls. Known pull roll arrangements are nip rolls, s-wrapped pull rolls, omega-wrapped pull rolls and vacuum rolls which are described in the following more in detail.
The purpose of pull roll is to transport the web within a machine or plant. Therefore these rolls have to be driven and the torque of the roll(s) have to be transmitted with minimum loss of friction (slippage) between roll surface and the web. To reach this, different types of pull rolls are available:
S-wrapped pull rolls
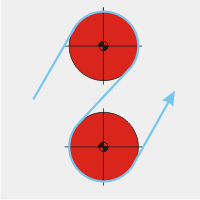
Here the web is guided around the rolls in a s-shaped way, were the rolls are arranged with a fix distance to each other. Both rolls are driven and the rolls have a surface with a good grip (i.e. they are rubberized). The principle of the s-wrapped pull rolls is according to the rope friction principle. This means in front and behind the pull rolls a suitable tension has to be within the web. With s-wrapped pull rolls a tension difference of approx. 1:2 can be achieved.
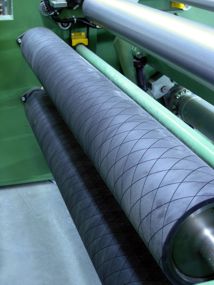
S-wrapped pull rolls
Omega-wrapped pull roll
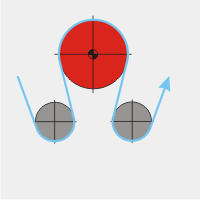
This type of pull roll is very similar to the priciple of the s-wrapped pull rolls: By two idler rolls the web is guided around the driven pull roll omega-shaped. The pull roll has a surface with a good driving effect of the web. Also here a tension has to be within the web before and after the pull roll in order to ensure a friction free troque transmission from the roll to the web. With the omega wrapped pull roll a similar tension difference before and after the pull roll can be achieved as with the s-wrapped pull rolls.
Nip rolls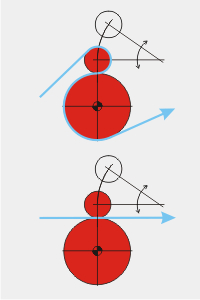
Here the web is guided between a driven pull roll and a pressure roll which is pressed against the pull roll. The web can either tangentially guided between the rolls or one of the rolls is partially wrapped by the web. One of the two rolls should have a softer surface than the other one (i.e. rubberized) in order to avoid any damage of the roll surfaces, when they are pressed together. As the transport of the web only depends on the pressure of the pressure roll, the roll surface is not relevant for this. So very high tension differences can be achieved before and after the nip rolls. Presupposition for the use of this nip rolls are the suitable material characteristics, which should not be damaged by the pressure with the nip of the two rolls.
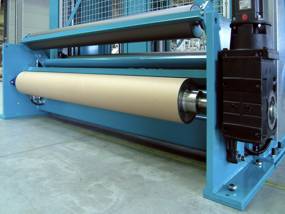
Nip rolls
Vacuum pull roll
Here the transportation of the web is achieved by a vaccum within the body of the roll. Through many holes on the rolls surface the web is sucked onto the roll surface in a certain area of the roll body and so a web transport is reached. Also here the material characteristics must allow such a transport (no or minimum air permeability, no damage of the material by sucking it onto the surface of the roll). Depending on the material characteristics and the resulting max. suction performance a relative high division of the tension before and after the vacuum pull roll can be achieved. Will be different web widths driven via the same vacuum pull roll, the not used holes besides the web shall be not active, as it will otherwise give a too high loss of vacuum performance. Because of the complex design of the roll this vacuum pull roll is an expensive solution compared with the other pull roll types.
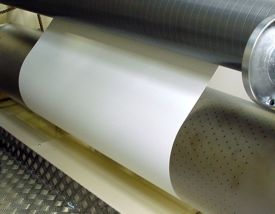
Vacuum pull roll