Winding encyclopedia
Here important terms of the winding technique were explained in alphabetical order. If you will have nevertheless still open questions, so we will answer these - please contact us.
At blade cutting the web is slit with an industrial razor blade for further processing.
The contact rolls lays onto the winding reel and thereby ensures a proper guiding of the web towards the reel. Additionally the trapping of air is avoided by the pressure between contact roll and reel (contact winding). Depending of the winding mode the contact roll can be driven or not driven.
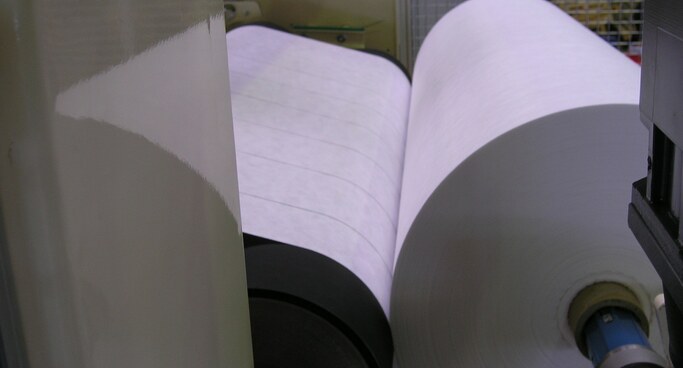
Contact winding
A dancer roll is used to generate a tension within the web and can be used for controlling a following drive (pull rolls, winder).
Friction winding is used to compensate diameter differences at multi-web winding on one common winding shaft. The diameter differences are the result of thickness differences of the web during production.
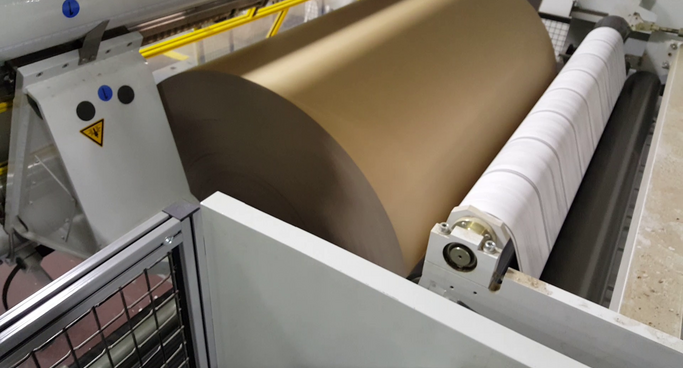
Gap winding
At the in-line production a web is continuously processed at non-stop operation. Therefore the reel change at an unwinder or rewinder has to be done within interruption of the production.
At the off-line production a web is processed discontinuously at start-stop operation. Therefore the reel change at an unwinder or rewinder can be performed at zero speed of the web.
Pull rolls are driven and will be used for web transport. Thereby pull rolls are used for tension separation before and after these rolls. Known pull roll arrangements are nip rolls, s-wrapped pull rolls, omega-wrapped pull rolls and vacuum rolls which are described in the following more in detail.
Reel change systems are used at an in-line production for cross cutting of the web and for starting a new winding cycle.Reel change systems can also be used for an off-line production in order to shorten the reel change time of a manual reel change or to make such a manual change more safe.