Friction winding
Friction winding is used to compensate diameter differences at multi-web winding on one common winding shaft. The diameter differences are the result of thickness differences of the web during production.
Depending on the different types of materials and tasks SOMATEC uses several types of friction winding shafts, but does NOT manufacture such friction winding shafts. In case of any demand of single friction winding shafts please directly contact a corresponding supplier of such friction winding shafts. The following explanations are only for illustration of the friction winding principle:
Certain products (e.g. plastic films) cannot be produced with an equal thickness over the width. So the film can be thicker at the edges than in the center. These thickness differences are only some µm per layer but will summarize to some millimeters when such a film is wound with some hundred or thousand layers.
When such a film is slit into several single webs and wound on one common shaft, different diameters of each wound reel will be the result. So only the reel with the maximum diameter is wound under tension. In front of the other reels will be a slack of material due to the missing tension.
This effect occurs only at rigid films as soft materials will compensate the diameter differences by different stretching of the webs. So the web with the maximum winding diameter will be stretched so much, that the other webs with (theoretically) smaller diameters also will be wound with the actual tension. As long as the stretching of the film is within the quality limits, no additional effort is necessary to wind such individual webs on one shaft.
With rigid film such a compensation by stretching of the film is not possible. So here an artificial compensation is needed. This is done by allowing a certain slippage (frictioning) of each wound reel on the winding shaft in radial direction. The winding shaft thereby is driven with a minimum overspeed (max. 2 - 3%) as needed for the minimum reel diameter. Transmission of the winding torque is done by friction elements where the amount of the friction is adjustable. Normally this adjustment is done by pneumatic pressure.
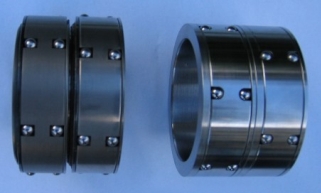
Several friction elements
Frictioning can either be done within the shaft with so called 'friction elements' (here usually a felt is used as friction surface) or frictioning is done between the inner core surface and a friction surface on the winding shaft. Clamping of the cores is done on the outer surface of the friction elements. Usually balls are used as clamping elements. They run obliquely and thereby clamping the cores when rotating the cores on the friction elements. Frictioning within a friction elements has the advantage of nearly constant conditions (independent of the core material and core dimensions). But the design of a friction winding shaft with friction elements is more complex and therefore such shafts are more expensive.
Direct frictioning between core and a friction surface on the shaft is much easier to realize (similar as a normal air shaft). The disadvantages of this principle are possible dust contamination by abrasion of the core material and a missing fixation of the cores to the sides. So stop-rings and spacers between the cores can be used for fixation of the core position but these elements are obstructive for an automated shaft handling.
Because of the described pros and cons friction shafts with friction elements are mainly used within slitters at Off-line production as here accuracy and minimum tolerances are more preferred. Friction shafts with a direct friction between core and a friction surface on the shaft are used more during In-line production for a pre-processing of the produced webs.