08/21/24
For sale and available: Automatic Turret Unwinder UW1200-1900 E
Turret unwinder for non-stop use for sale at short notice. Few operating hours as this is a demonstration machine for trade fairs. Machine can be inspected and tested.
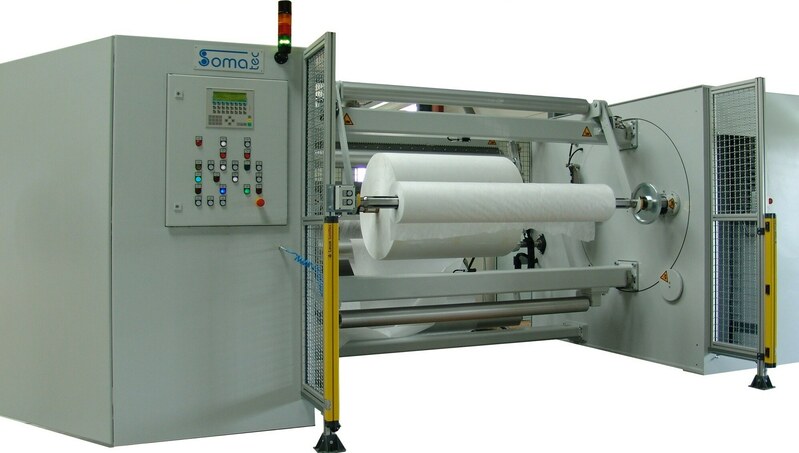
Technical Data:
- Year of manufacture 2005
- Max material width: 1,800 mm
- Roller width: 1,900 mm, surface belt-ground
- Production speed: max. 250 m/min
- Tensile force: 40 – 300 N
- Core diameter, inside / outside: 3“ / 90 mm and 6“ / 170 mm
- Core material: cardboard
- Core clamping: with pneumatically expanding winding shafts
- Unwinding diameter: max. 1,200 mm - min. 400 mm
- Roll weight: max. 600 kg
- Required compressed air: 6 bar
- Electrical voltage: 3 x 400 V / 50 Hz
- Control voltage: 24 V
- Machine operating side: left in WLR
- Drive side: left in WLR
- Labeling: German
Machine design:
- Turret unwinding machine with two winding stations
- The winding stations are mounted in two turret discs that are connected to each other by two cross beams. The stable turret discs are mounted on the circumference on support rollers in the side stands and are equipped with a gear ring. A gear brake motor positions the turning discs according to the turning position calculated on the basis of the measured roll diameter.
Each winding station is equipped with two pneumatically operated chucks to accommodate the winding shafts. When tensioned, the chucks are also mechanically locked. To align the new roll laterally, the rotating sleeves can be manually adjusted axially by +/- 25 mm using a handwheel. - Each winding station is driven by a Siemens AC motor. The drives are housed in a closed side stand. The drive connection to the winding stations is via gears and toothed belts. The drives are controlled by a pendulum roller system arranged on the product outlet side.
- Automatic web connection system. Stored in a separate frame for swiveling from above. After the "web connection" command, the unit swivels down and presses the web that is running out onto the new roll of material, which has been accelerated to product speed. The beginning of the new roll of material must be specially prepared for this process so that the web connection can take place.
The running out web of the "old" roll is severed by a finely toothed knife.
An overlapping web connection is created. - Roll lifting device. With the help of this device, it is possible to lift a roll equipped with a winding shaft from the floor and guide it into the sleeves. To do this, the turning position is changed at the push of a button while the other roll is unwinding until the two hooks reach the new roll and lift it up. This process is not automatic.
The previously listed assemblies are housed in sturdy, welded steel stands that are easily accessible from the sides through double doors. The web guide rollers used are not driven, made of aluminum, belt-ground. The control panel is integrated in the left side stand.
Electrical design:
- Siemens S7
- The turret drive is operated with an AC motor and servo inverter.
- The winding drives are operated with asynchronous servo motors with servo inverters.
- The unwinding motors are operated with speed control, whereby a correction signal from a pendulum position controller compensates for tension fluctuations.
The unwinding diameter is recorded by ultrasonic sensors. - The deflection roller in the cutting system is not driven.
- The operation is equipped with a color operator panel OP27 and hardware control devices.
- The operator panel is used to enter setpoints, display actual values and messages.
- Operating voltage: 3 AC 400V 50/60Hz
Auxiliary voltage: 230V 50Hz
Control voltage: 24VDC
Humidity: 60%
Ambient temp. : 35 degrees - Software for S7, OP, and drives.
Documentation language S7 / OP27 German or English. - The control and regulation devices are installed in a separate control cabinet.
Price on request. Retrofit and CE re-issuance possible on request. Contact us. sales@somatec-hameln.de